MRT's Complete Range of Services
- Design Design
- Tooling Tooling
- Pressure Pressure
- Gravity Gravity
- Sand Sand
- Machining Machining
- Surface Finishing
- Assembly Assembly
- Logistics Logistics
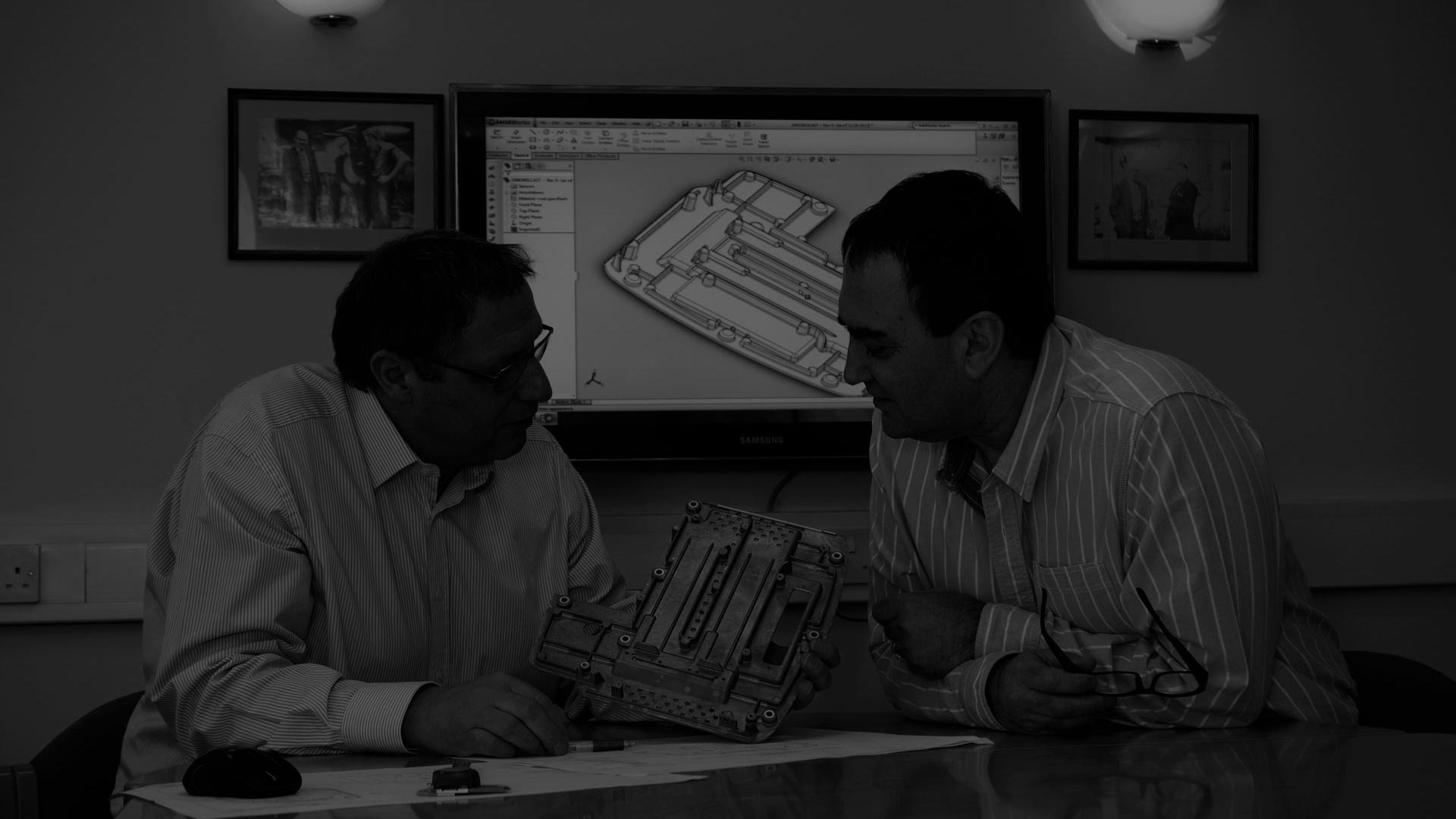
You have a vision for a new product.
You know the functionality and the aesthetics which you need but unless your product can be manufactured economically, repeatably, reliably and within the correct timeframes it will never achieve its full potential.
MRT's technical team have been designing successful cast components for many decades. We work in partnership with your product designers to develop and adapt your concept or design to optimise it for manufacture. We use our experience, expert knowledge, and the latest Solidworks CAD modelling and Magmasoft casting simulation software to help us achieve innovative designs in partnership with our customers, which can be manufactured within the controlled parameters required.
Designing castings is a specialist skill. Die cast components require specific features such as draft taper, even wall thicknesses, and the avoidance of undercuts and isolated heavy sections. All of these issues can be easily overcome if you work directly with our team before you freeze your design. Costs of machining, surface finishing and assembly can also be dramatically reduced if we are consulted early in the design process.
MRT have been manufacturing high quality components for over 75 years. It's the experience, techniques and tricks of the trade that we have developed over that time that we will share with your designers and engineers to optimise your products.
MRT specialise in complex components for demanding applications. Consistent and repeatable components require advanced process control and meticulous design. We will explain the features needed to ensure excellent finish and dimensional accuracy.
MRT operate SOLIDWORKS and FUSION with POWERSHAPE as our CAD packages, alongside MAGMASOFT, the foundry industry's most powerful and respected casting simulation software. We have resources for producing prototypes for evaluation and testing prior to committing to production tooling.
Where required, MRT can prepare full component drawings, solid models, manufacturing and finishing specifications.
Find out more information about MRT Castings and get a taste of our facilities.
Check out our virtual tour and find out how we can work with you on your next project.
I want...
We’re all enjoying the summer weather right now, but at MRT we’re putting the sunshine to great use.
Read MoreWe're excited to announce that MRT Castings will be exhibiting again at Southern Manufacturing & Electronics!
Read More17th Jul 2023
MRT Castings is proud to announce that it has achieved certification to the ‘Cyber Essentials Plus’ standard.
Read More© MRT Castings Limited 2025 | Registered in England - No. 3150165 | VAT No. GB 199 1318 33