MRT's Complete Range of Services
- Design Design
- Tooling Tooling
- Pressure Pressure
- Gravity Gravity
- Sand Sand
- Machining Machining
- Surface Finishing
- Assembly Assembly
- Logistics Logistics
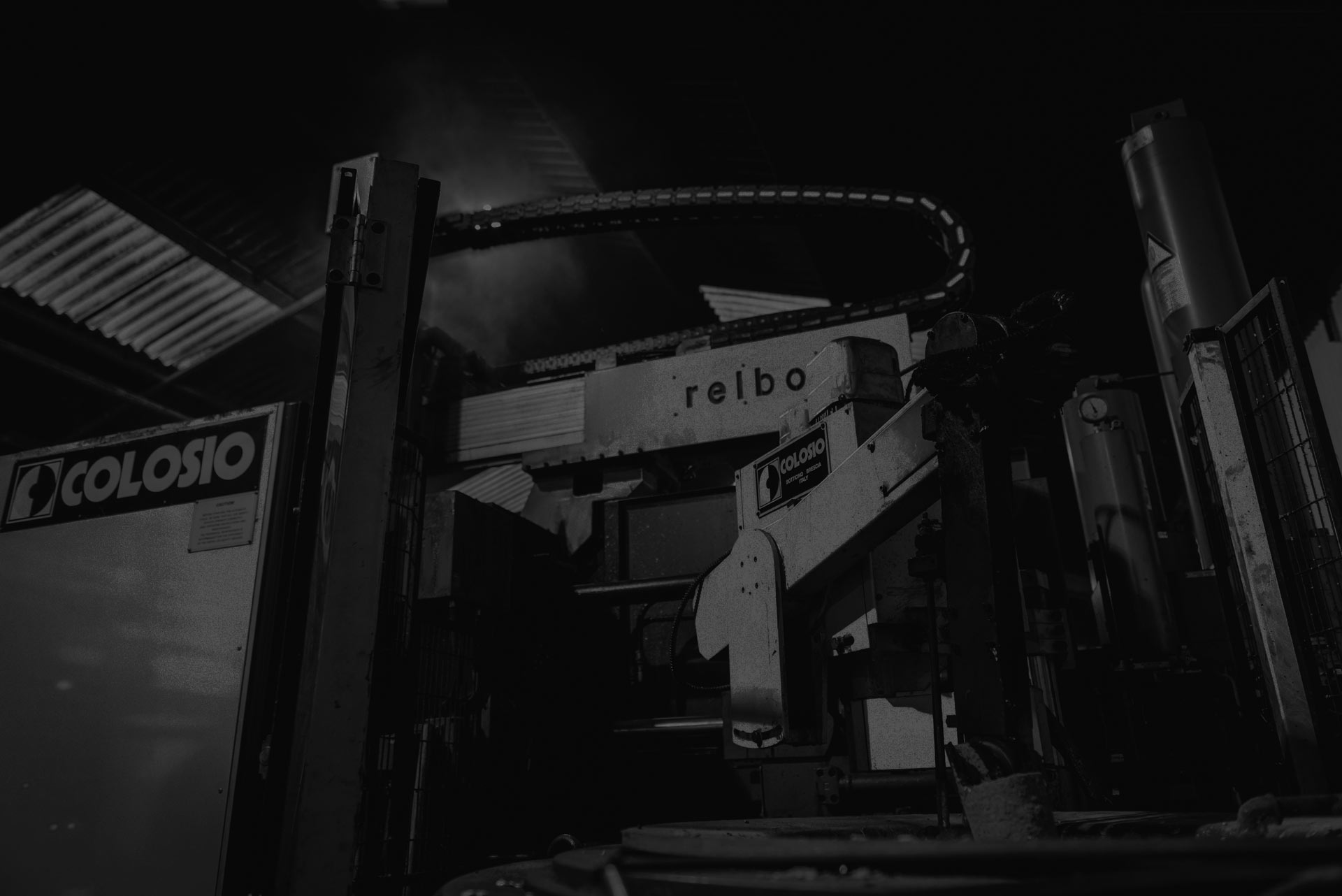
High pressure die casting provides the shortest route from molten metal to completed component, by injecting molten metal into a hardened steel mould and allowing it to solidify under pressure before ejection.
The process allows fast, precise, cost effective production of aluminium die castings, meeting the needs of hi-tech industries where product appearance and dimensional tolerances are critical. MRT have high pressure die casting machines with locking forces of between 220 and 530 tonnes. All feature computerised real-time shot control, automatic ladling, die-spray, automatic casting extraction and cooling.
Small Quantities? - No Problem! Many pressure die casting foundries only offer their services for high volume orders, claiming that lengthy set-ups make the process prohibitive to small quantities of aluminium die castings. MRT have optimised their tooling preparation and set-up operations to make the process more accessible to customers who require only small quantities, but whose applications would benefit from the excellent dimensional and cosmetic properties of pressure die casting. So, MRT can provide the complete service, whether you require a batch of 10 or 10,000.
Accessibility Controls
The player supports TAB to change the controls.
Update Required<br/>To play the media you will need to either update your browser to a recent version or update your <a href='http://get.adobe.com/flashplayer/' target='_blank'>Flash plugin</a>.
Real-time shot control systems, and comprehensive set-up records and quality data ensure consistent production and reduce pressure die casting set-up time.
Quality is achieved by pride in workmanship, backed up by an excellent quality system to ISO9001. For critical components, MRT can provide X-ray, dye penetrant and pressure testing.
Routine tool maintenance, breakdowns and modifications can all be undertaken in-house to reduce tool down time.
We can help you optimise designs, eliminating elements which add unnecessary costs. Where required, we can also provide filling and solidification simulations using Magmasoft.
Find out more information about MRT Castings and get a taste of our facilities.
Check out our virtual tour and find out how we can work with you on your next project.
I want...
We’re all enjoying the summer weather right now, but at MRT we’re putting the sunshine to great use.
Read MoreWe're excited to announce that MRT Castings will be exhibiting again at Southern Manufacturing & Electronics!
Read More17th Jul 2023
MRT Castings is proud to announce that it has achieved certification to the ‘Cyber Essentials Plus’ standard.
Read More© MRT Castings Limited 2025 | Registered in England - No. 3150165 | VAT No. GB 199 1318 33